Collaborative robots, often referred to as “cobots,” are a type of robotic technology designed to work alongside humans collaboratively and interactively. In our previous article, top 7 Manufacturing Trends to watch out for, we have briefly studied cobots. This article will present in-depth information about cobot applications, features, and their programming.
What are cobots
As already discussed, cobots are a tool to augment human capabilities, improve efficiency, and enhance workplace safety. Refer to the below specifications of cobots:
- Safety Features:
- These are equipped with advanced safety features such as force and torque sensors that enable them to detect and respond to external forces, ensuring safe collaboration with human workers. This eliminates the need for physical barriers or safety cages.
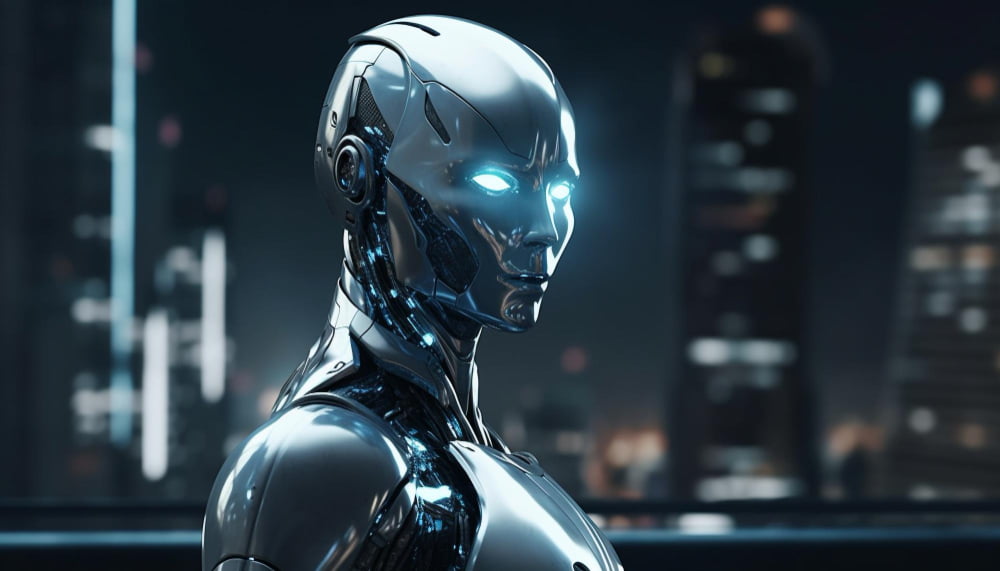
Read more, how to build robots using two fundamental elements.
- User-Friendly Interface:
- Cobots are easily programmable by individuals with varying levels of technical expertise. Many cobots feature intuitive interfaces that allow users to teach or program the robot through simple and user-friendly methods.
- Flexible Deployment:
- These are versatile and can be quickly reprogrammed or redeployed for different tasks. This flexibility makes them suitable for environments with changing production needs.
- Sensitivity to Surroundings:
- Cobots have sensors, cameras, and other technologies to perceive their surroundings. This enables them to adjust to active environments, avoid obstacles, and cooperate effectively with human coworkers.
- Force Limiting:
- They are designed to limit their force and speed when in contact with humans. This ensures that any contact is safe and minimizes the risk of injury.
- Various Payload Capacities:
- Collaborative robots come in different sizes and with varying payload capacities, allowing them to handle a wide range of tasks. Some cobots are lightweight and suitable for jobs that require precision, while others have higher payload capacities for heavier-duty applications.
- Applications Across Industries:
- Cobots are used in various industries, including manufacturing, healthcare, logistics, agriculture, and more. They can be used for tasks such as assembly, material handling, quality inspection, and even medical surgeries.
- Human-Robot Collaboration:
- Cobots are specifically designed to work in close collaboration with human workers. This collaboration can take various forms, from working side-by-side on assembly lines to assisting with tasks that may be physically demanding or hazardous.
- Cost-Effective Automation:
- These are often more cost-effective than conventional industrial robots. Their ease of use and adaptability make them accessible to a wide range of businesses, including small and medium-sized enterprises.
Read our post on Tesla Robot Optimus: is it a pioneer of a new era.
Major giants in cobot manufacturing
In terms of the largest cobot production, it’s challenging to pinpoint a single leader as the industry is global, with different countries contributing significantly. Historically, countries such as Denmark, Japan, Germany, and the United States have been at the forefront of collaborative robot development and manufacturing. However, China has also emerged as a major player, with several Chinese companies actively participating in the production of collaborative robots.

Universal Robots (Denmark)
Universal Robots is often considered a pioneer in the field of collaborative robotics. They are known for their user-friendly cobots that are easily programmable and can be deployed for different domains.
ABB (Switzerland/Sweden)
ABB, a multinational corporation headquartered in Switzerland and Sweden, is a major player in this field. They produce a range of industrial robots, including collaborative robots like the ABB YuMi series.
Fanuc (Japan)
Fanuc, based in Japan, is a global leader in industrial automation, including the production of industrial robots. They have a presence in various industries and offer both traditional and collaborative robots.
KUKA (Germany)
KUKA, a German company, is renowned for its robotics and automation solutions. They provide a range of robotic systems, including collaborative robots designed for safe interaction with humans.
Yaskawa (Japan)
Yaskawa, another Japanese company, is a significant player in the sector. They manufacture industrial robots, including cobots, and have a strong presence in automation technologies.
Techman Robot (Taiwan)
Techman Robot is a Taiwanese company known for its collaborative robot solutions. They focus on user-friendly programming and versatility in various applications.
Doosan Robotics (South Korea)
Doosan Robotics, based in South Korea, is gaining recognition for its cobots designed for precision and ease of use. They offer a range of cobot models suitable for different industries.
Cobalt Robotics (United States)
Cobalt Robotics, based in the United States, specializes in security and surveillance robots. While not exclusively focused on manufacturing, their robots play a collaborative role in human-centric environments.
HAN’S Robot (China)
HAN’S Robot, part of the HAN’S Laser Group in China, is making strides in the field of collaborative robotics. They offer cobots with various payload capacities for different applications.
How to program cobots
Programming collaborative robots (cobots) involves specifying the sequence of tasks and movements that the robot should perform. One of the vital advantages of cobots is their user-friendly programming interfaces, which allow individuals with varying levels of technical expertise to program and operate them. The specific programming methods may vary among different cobot manufacturers, but here is a general guide on how to program them:
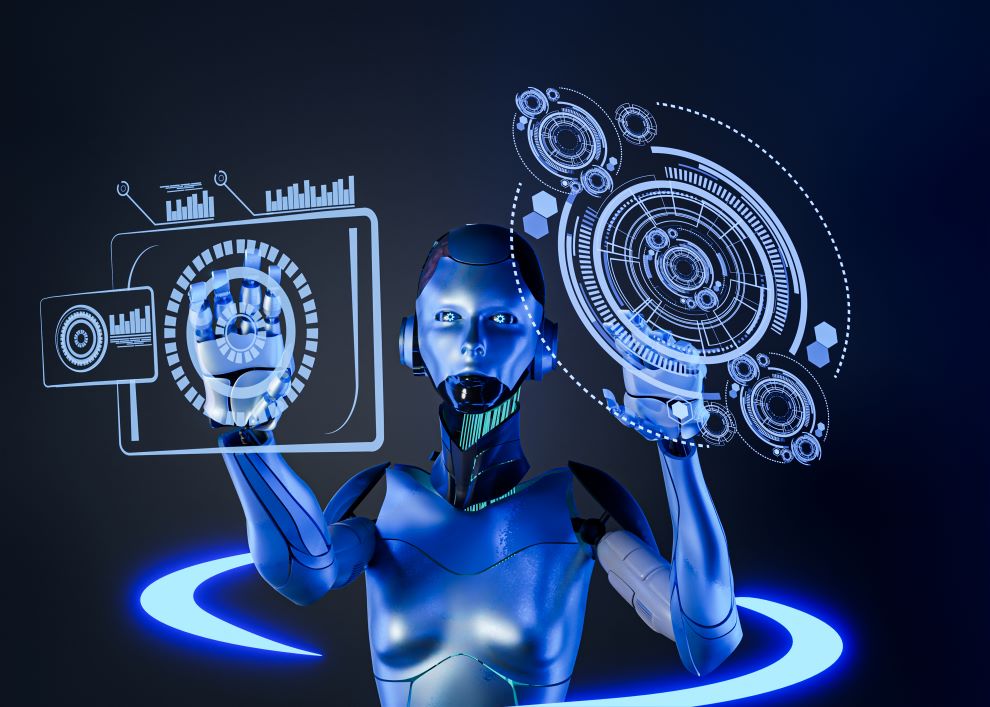
Teach Pendant Programming
Many cobots come with a teach pendant, a handheld device that allows users to manually guide the robot through the desired motions. This method is often called “teach and repeat.” Users move the cobot through the required path, and the robot records the positions.
Graphical User Interface (GUI)
Cobots often feature graphical user interfaces that simplify the programming process. Users can drag and drop commands, set waypoints, and define actions through an intuitive graphical interface, eliminating the need for complex coding.
Waypoint Programming
Waypoint programming involves specifying key points (waypoints) that the cobot should reach during its operation. Users can define these points by physically moving the cobot or inputting coordinates through the programming interface.
Scripting and Programming Languages
Some cobots allow users to program using scripting or programming languages such as Python or a proprietary language. This is typically more advanced and is suited for users with programming experience.
Offline Programming
Some cobot systems offer offline programming capabilities. Users can create and simulate robot programs on a computer without the need for a physical robot. Once the program is verified, it can be transferred to the actual cobot.
Task-Based Programming
Cobots may support task-based programming, where users define specific tasks the robot should perform (e.g., pick and place, assembly) rather than focusing on individual motions. This approach simplifies the programming process for users who need deep technical knowledge.
Sensor Integration
If the cobot is equipped with sensors (such as vision systems), programming may involve configuring these sensors to enable the robot to respond to its environment. This can include object recognition, tracking, and other sensor-based interactions.
Refer to our article on introducing LiDAR: a complete guide if you are interested to learn about LiDAR sensors.
Safety Programming
Collaborative robots prioritize safety, and programming should include defining safety parameters. This may involve setting limits on robot speed, and force, and defining safe zones to prevent collisions with humans or other obstacles.
Testing and Debugging
After programming, it’s essential to thoroughly test and debug the cobot program. This can be done in simulation or with the actual robot, ensuring that the robot performs tasks accurately and safely.
Documentation and Training
Document the programmed tasks and provide training for operators and other relevant personnel. This helps in the smooth operation and maintenance of the cobot system.
Continuous Improvement
Regularly review and update cobot programs as needed. Continuous improvement ensures that the robot adapts to changes in the production environment or task requirements.
Keep in mind that specific programming methods may vary based on the manufacturer and model of the cobot.
Continuous improvement or Kaizen is an essential part of any process in the industry.
Also read, 8 practical Kaizen ideas to implement in a company.
Cobot industrial applications
Manufacturing and Assembly
- Precision Assembly: Cobots excel in tasks that require precision and repeatability, such as assembling electronic components or intricate machinery.
- Small Parts Handling: They are adept at handling small parts in manufacturing processes, reducing errors and increasing throughput.
Material Handling and Logistics
- Pick and Place: Cobots can efficiently pick items from one location and place them in another, streamlining material handling processes.
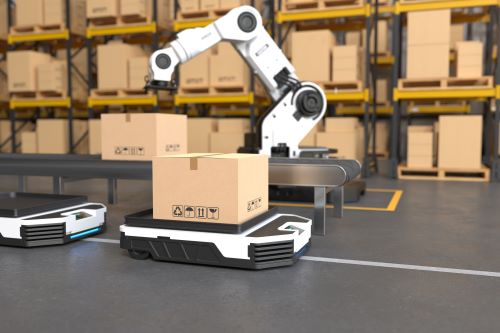
- Palletizing and Packaging: Cobots are used for palletizing goods and packaging, reducing the physical strain on human workers and improving overall efficiency.
Quality Inspection
- Vision Systems Integration: Cobots equipped with advanced vision systems can perform quality inspections, identifying defects in products and ensuring high-quality output.
Refer to our article on 15 most valuable terms to understand ISO 9001:2015, if you are interested to learn about quality management system.
Welding and Cutting
- Collaborative Welding: Cobots are employed in welding applications, working alongside human welders to increase productivity and ensure precise welds.
- Material Cutting: They can be used for laser cutting or other material cutting processes, providing accuracy and speed.
Painting and Coating
- Collaborative Painting: Cobots equipped with painting or coating tools assist in applications where a uniform and precise coating is required.
Machine Tending
- CNC Machine Tending: Cobots can tend to CNC machines, loading and unloading parts, minimizing downtime, and improving overall machine utilization.
Testing and Inspection
- End-of-Line Testing: Cobots are utilized for end-of-line testing and inspection processes, ensuring that products meet quality standards before reaching customers.
Medical and Healthcare
- Assistance in Surgeries: Cobots are used in medical settings to assist surgeons in performing delicate and precise tasks.
- Laboratory Automation: They play a role in automating laboratory tasks, handling samples, and performing repetitive procedures.
Agriculture
- Harvesting and Sorting: Cobots can be employed in agriculture for tasks such as harvesting crops and sorting produce.
Food and Beverage Industry
- Food Packaging: Cobots are utilized for packaging in the food and beverage industry, ensuring hygiene and precision.
Construction
- Bricklaying and Construction Tasks: Cobots can assist in tasks like bricklaying, reducing labor-intensive work and improving efficiency.
Education and Research
- Research and Development: Cobots are used in research settings for various tasks, allowing researchers to focus on the analytical aspects of their work while cobots handle repetitive tasks.
These applications demonstrate the versatility of cobots across industries, offering a collaborative and adaptable solution to various tasks traditionally performed by humans or conventional industrial robots.