The latest manufacturing trends are essential to survive and thrive in this digital age. Rising business opportunities, technological revolutions such as IoT, and growing customer requirements are a few reasons to upgrade manufacturing methods in an industry. Many companies are evolving in this digital transformation for sustainable growth in the future.
Cobots
Cobots are collaborative robots that work with humans in factories or workspaces. J. Edward Colgate and Michael Peshkin in 1996 designed this technology. Cobots primarily perform tasks such as packaging, assembly, quality control, material handling, and other tedious jobs. According to the latest survey by Statista, the global cobot market is worth $923.7 million.
Because of low power requirements, cobots are used in industries such as Electronics, Healthcare, Supply chain management, Automotive, fabrication, food processing, etc.
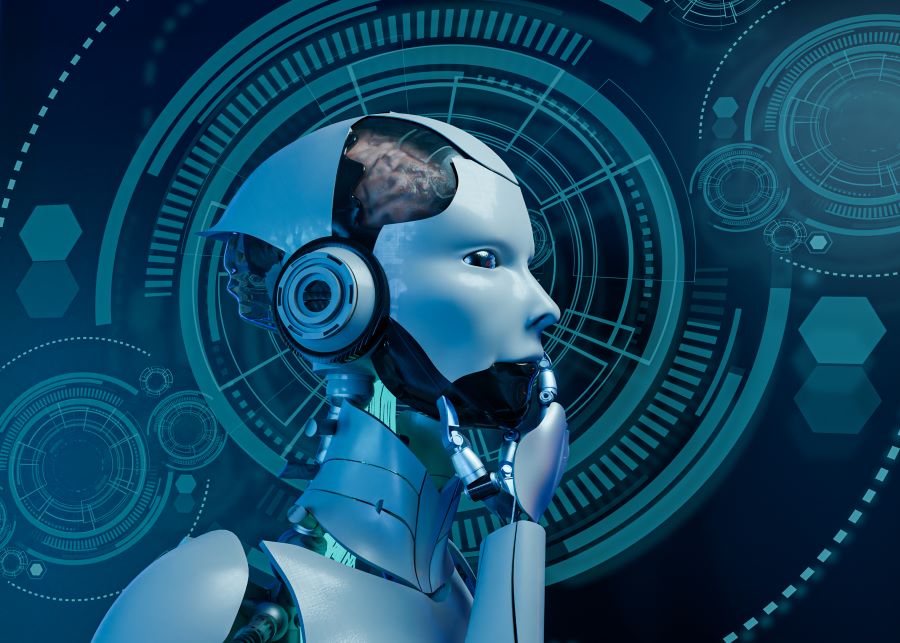
If you are interested to know about material handling in factories, refer to our article on how to distinguish between Inventory and Stocks.
How does cobots work
Cobots have software-managed sensors that identify people, objects, and probable strikes on the way. These sensors can also detect unfamiliar actions and stop cobots instantly. Generally, industrial cobots have built-in sensors to identify unusual forces or unpredictable crashes. These sensors slow them down or stop their work to control accidents. Latest technologies like pattern recognition, vision cameras, LED sensors, and machine learning can also avoid such threats.
Read more, introducing LiDAR: a complete guide.
Cobots are one of the accurate and flexible manufacturing trends. Additionally, they maximize productivity and ensure human safety by performing tedious and dangerous tasks.
Predictive maintenance
Predictive maintenance is one of the top AI Trends in the Automotive Industry. It improves the performance and health of any machine or instrument by constantly evaluating its condition in real-time. It can recognize, spot, and handle errors by implementing advanced trends such as machine learning and analyzing sensor data. Furthermore, it can also examine potential future issues that can occur. Predictive maintenance is widely used in energy, automotive, telecommunication, smart cities, and manufacturing sectors. The market size of predictive maintenance was worth $5.93 billion in 2023, per the latest survey.
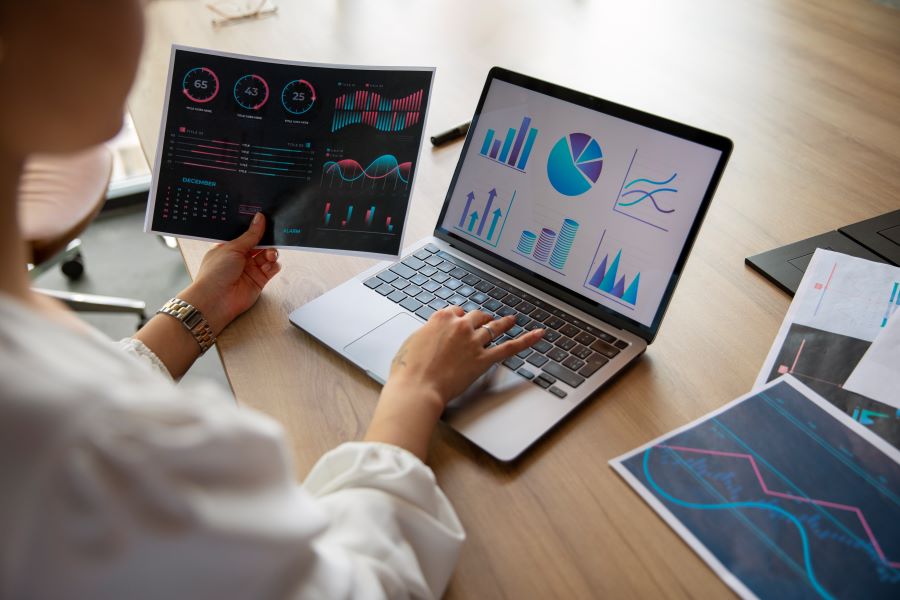
Predictive maintenance as a manufacturing trend
Predictive maintenance can be considered a combination of AI (artificial intelligence), IoT, and predictive analytics. Initially, the data is recorded from the sensors installed on machines in the computerized maintenance management system (CMMS) or enterprise asset management (EAM). Then, the data analysis takes place that gives insights about the equipment. Due to AI and machine learning, it is possible to know the potential defect warnings and prediction of future conditions of equipment. This technology is highly beneficial in lean manufacturing supply chains, and work scheduling is vital. ABB, Honeywell, Dingo, and PTC are some of the major players in this sector.
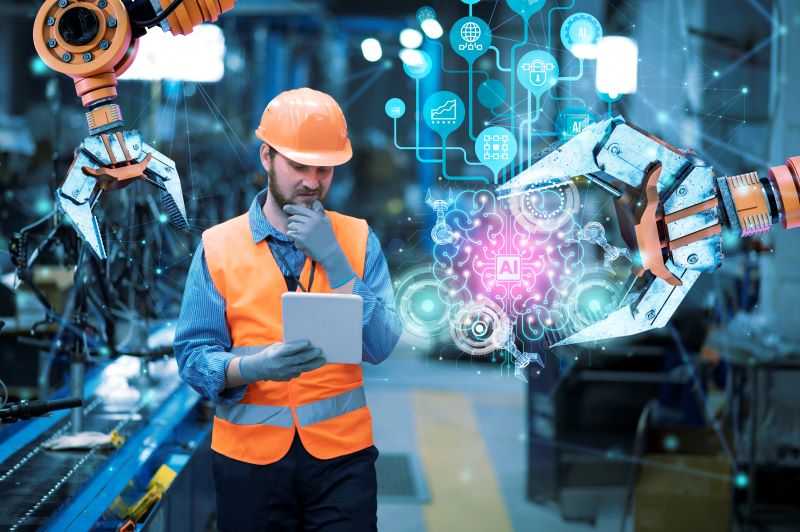
Digital twins
Digital twins serve as a reliable substitute for the real-world objects they represent. They are customized for each item instead of a generic representation of a category. It’s worth noting that even if two products appear identical, their digital twins will still have distinct characteristics and won’t be completely the same. Although it’s common for digital twins to have a visual representation like a 2D or 3D CAD image, visual elements are not always necessary. The digital model can be a database, a collection of equations, or even a spreadsheet. This versatility allows for more flexibility and diverse applications in various industries.
According to a recent survey, the digital twin market was valued at $10.25 billion in 2022. IBM, Siemens, and Cisco Systems are a few of the giants in the digital twin market.
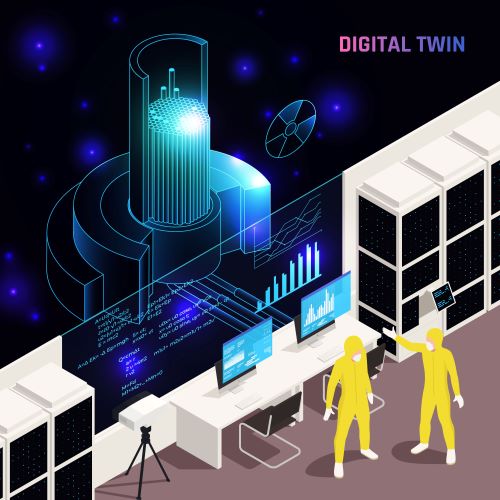
Working principle of digital twins
Digital twins use the same CAD and modeling software used by designers and engineers during the initial stages of product development. It allows for a seamless virtual replication of physical products, enabling businesses to optimize their designs and processes. Companies can streamline their workflows, reduce costs, and deliver superior products to market. The entity and its twin are linked through IoT sensors through a proper IoT framework. Digital twins are significant manufacturing trends for IoT as they provide structure, analytics, and usability to disorganized and difficult-to-interpret IoT data.
If you are curious to know more about IoT, read these IoT FAQs.
Smart factory
A smart factory is a modern industrial facility incorporating advanced technologies and digitalization to optimize manufacturing operations. It leverages trends such as artificial intelligence (AI), machine learning, Internet of Things (IoT), robotics, big data analytics, and cloud computing to create a connected and intelligent ecosystem. The primary goal of a smart factory is to improve productivity, efficiency, and flexibility while reducing costs and waste. It combines various processes, from the supply chain to the shop floor into a cohesive network of interconnected systems.
In 2022, a staggering amount of $107.3 billion in revenue was recorded for the smart factories. It is expected to grow to $256.5 billion by 2032, as per the report of DataHorizzon Research. It is dominated by big players such as Siemens, Bosch, Mitsubishi Electric, Honeywell, etc.
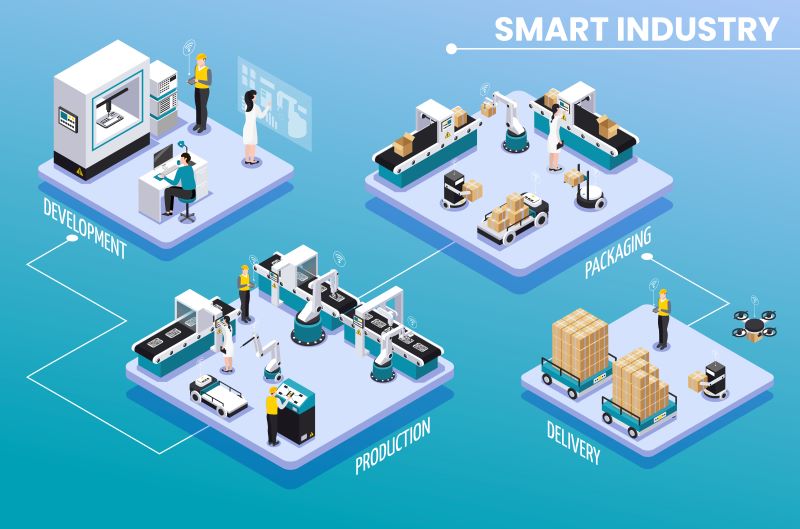
Imagine a cutting-edge digital factory that operates by bringing machines, people, and Big Data into one digitally interconnected ecosystem. This advanced setup doesn’t just stop at curating and analyzing data; it goes further by continuously learning from experience. This manufacturing trend analyzes data sets to predict future trends and circumstances. Additionally, it enforces manufacturing workflows and processes.
Industry 5.0
Industry 5.0 is the next iteration of Industry 4.0 as it advances this technology by increasing interaction between humans and robots. Industry 5.0 focuses on human potential by elevating technology to cater to humans. It wants to use creativity and the criticality of human thoughts to build robots accordingly. Furthermore, it also works to protect the environment by reducing emissions, energy consumption, and waste. It also emphasizes utilizing green energy. Industry 5.0 is still in its infancy with great potential to grow and expand.
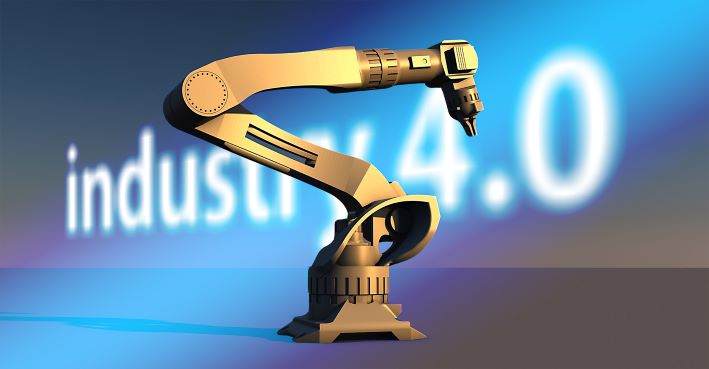
It is building a human-centric strategy by collaborating with industry 4.0 trends such as cybersecurity, additive manufacturing, augmented reality, cloud computing, etc.
Generative AI
OpenAI, BentoML, Pinecone, etc., are a few examples of generative AI that took the world by storm. It is a new AI trend that can produce high-quality text, audio, and imagery. The generative AI market is projected to reach $44.89 Billion by the end of 2023.
It needs input in the form of an image, text, a design, or anything else that can be processed with AI. AI then processes the output with the help of algorithms. It can include articles, deep fakes, audio, and solutions to the inputs. Anyone can ask GenAI using plain language. Modifying the result with feedback about quality, genre, creativity, tone, and other possible things is possible.
Generative AI models such as natural language processing (NLP) can recognize the data patterns and responses accordingly with the new output data. ChatGPT, Bard, and Dall-E are just a few examples of this tool, revolutionizing how we create and interact with information.
Extended reality
Extended Reality (XR) is a combination of Virtual Reality (VR), Augmented Reality (AR), and Mixed Reality (MR) that represents a paradigm shift in human-machine interaction. XR technologies alter how we perceive, interact, and collaborate with information by closing the gap between physical and digital reality. Philips, Accenture PLC, Qualcomm Technologies Inc., Softweb Solutions Inc., Varjo Technologies OY, SphereGen Technologies, Microsoft Corporation, and Apple are a few top companies in the world of XR.
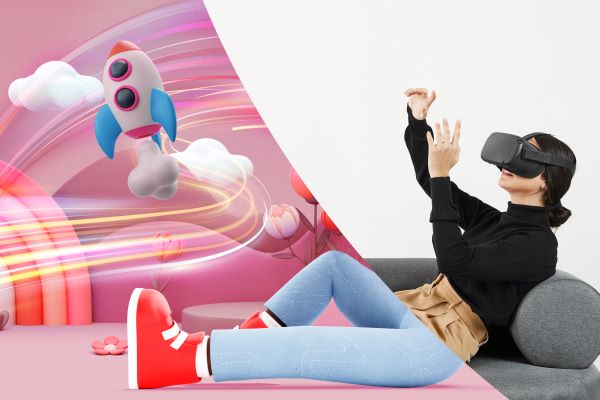
How does extended reality work
Within VR, immersive environments surpass the limitations of physical space, enabling users to explore virtual landscapes, engage in simulated experiences, and foster deeper levels of engagement and presence. AR allows users to access contextual data, enhance physical objects with digital overlays, and seamlessly integrate technology into everyday activities. MR creates a hybrid reality where virtual objects can interact with and respond to the physical environment, opening up new design avenues, prototyping, and collaboration.
The implications of XR extend far beyond mere entertainment, reaching into diverse fields such as education, healthcare, training, design, and engineering. Imagine surgeons performing complex procedures with holographic guidance, students exploring historical events through immersive simulations, or engineers collaborating virtually on real-time projects. XR technologies can revolutionize the way we learn, work, and interact with the world around us.
Please write to us in the comment section if you want to know about other manufacturing trends.